One of our customers is an aviation company producing engine parts that go into the US military’s UH-60 Black Hawk tactical transport helicopters. Black Hawks have been around since the 1970’s and have had a lot of engine modifications over the years. Due to all these changes, the company has to inventory a wide variety of parts that require aviation labels.
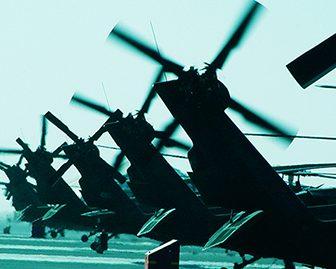
Working with the government, they implemented some processes to cut back on their inventory problems. As a first step, they developed a retro-fit kit. Once installed, these kits result in all of the helicopters having the same parts list, regardless of their age or model. Off to a good start!
During development of the retro-fit kit however, paperwork containing important information about each part often became detached. Those valuable records would be lost—simply because labels with adhesives weren’t allowed.
One step forward, two steps back…
The contractor decided they wanted a tag that didn’t have adhesive. One that could be attached to the part without accidentally coming off in transit. The tag also had to be easy to remove by hand because tools—such as scissors—weren’t allowed due to strict regulations.
The third obstacle they faced was the amount of human error generated in recording all that part data. For instance, production personnel entering serial numbers occasionally swapping letters and numbers. Without accurate data, the parts could not be installed and would delay production until the correct information was retrieved. What would their solution look like? They needed a barcode system allowing them to scan and print their information fast and accurately! We proposed a Zebra industrial label printer and BarTender® Professional software that easily ties into their database.
It was the fourth and final obstacle which proved to be a head-scratcher! With many facilities around the world, they were also building parts for jet engines. The size of the parts varied and they needed a range of tag sizes from 18 to 45 inches long. They didn’t want to keep a huge inventory of tags in a lot of different sizes—they wanted a one-size-fits-all solution.
Creativity in The Approach
After some creative thinking, the Innovation team at EIM came up with the idea to use our rugged #448 Plastic Tag material. This product does not have an adhesive so we avoided the whole issue of sticking to engine parts. To make this a single tag solution, we make their tags with perforations and sensing slots every 9 inches. When they need an 18 inch tag, they simply let their printer advance 2 sensing slots to get an 18 inch tag. For longer tags, they just print according to the correct number of sensing slots, allowing tags up to 45 inches in length.
The tags are designed with perforations so they can be easily ripped apart, but are strong enough to suspend 12 pounds without tearing! The #448 tags are thermal transfer printable, so this manufacturer can print their own barcodes (and other critical information) on-demand and on-site. Designed to be secured with a plastic snap, these tags were adhesive-free and easily removed by hand!
A Black Hawk pilot tagging program using our tags is now being used in two locations for F-18 Super Hornets. They have since added a 14 inch tag version to extend the length of their tags. Once the part pilot was completed, the tags were implemented worldwide, on many more parts! Learn more about our OEM part labels.