You’re overseeing a vaccine production line where dozens of glass vials roll past at breakneck speed. Each vial contains a life-saving product, yet without clear, accurate labels, these vials could be rendered virtually useless. Regulatory compliance becomes harder to manage, and traceability from manufacturing to distribution is compromised.
Vaccine labeling is a vital piece of the puzzle, ensuring that every dose is identified correctly, tracked efficiently, and administered safely. But how can you be sure your labeling strategy meets stringent standards for adhesion, legibility, and security at every stage of the supply chain?
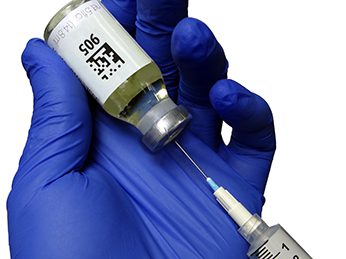
The Importance of Accurate Vaccine Labeling for Traceability
When dealing with vaccinations, the stakes are extraordinarily high. Everything—from the vaccine’s lot number and expiration date to batch data—must be crystal clear. Incomplete or illegible labels can lead to costly recalls, misadministration, or even risks to patient safety. On top of this, global regulators have raised the bar for vaccine distribution, demanding full traceability from production lines to final immunizations.
Accurate labeling matters for:
- Regulatory Compliance: Authorities like the FDA, EMA, and WHO have strict guidelines for labeling and tracking vaccine doses.
- Patient Safety: Accurate labels help healthcare professionals confirm vaccine identity and expiration, minimizing the risk of errors.
- Counterfeit Prevention: Clear labeling, often with security features, discourages counterfeiting in a global market.
- Efficient Recalls: If a recall is needed, well-labeled vaccines allow quick identification of affected batches, saving time and reducing the likelihood of distribution errors.
Common Challenges in Vaccine Labeling
Vaccine manufacturers and distributors face a host of labeling issues that can threaten traceability. Addressing these challenges at the outset helps ensure a smooth process and lowers costs tied to rework or recalls.
- Adhesion to Glass Vials: Glass has a non-porous surface, meaning standard adhesives can peel or slip off easily, especially in cold or moist environments.
- Legibility in Low Temperatures: Vaccines often require refrigeration or freezing, conditions that can lead to condensation or frosting, obscuring text and barcodes.
- Risk of Tampering: Labels must show clear evidence if someone attempts to open or alter a vial, especially in high-stakes vaccination campaigns.
- Barcode Accuracy: Even a slightly smudged or damaged barcode can cause scanning failures, slowing down distribution and creating data blind spots.
- Storage Durability: Extended shelf-life vaccines may remain in storage for months, demanding that labels retain both adhesion and clarity for the entire period.
Key Features of High-Quality Vaccine Labeling
What sets excellent vaccine labeling apart from run-of-the-mill stickers? At a high level, these labels combine advanced materials and adhesives, clear text or barcodes, and built-in security elements. Let’s break down some features that matter most for traceability and compliance.
Durability and Precision in Pharmaceutical Labeling
In the realm of pharmaceutical labeling, durability is king. Labels must endure temperature swings, exposure to moisture, and constant handling without losing readability or adhesion. Additionally, precise printing methods—often with thermal transfer or specialized digital presses—help maintain high-resolution text, scannable barcodes, and sharp logos.
Security and Integrity for Tamper-Evident Seals
Tamper-evident features—such as perforations or void-pattern adhesives—provide a layer of security that standard labels lack. If someone tries to remove or reseal the label, the tamper-evident design ensures visible evidence of meddling. This is especially important for preventing counterfeit or unauthorized distribution of vaccines.
Improving Traceability With Thoughtful Labeling
Consider a mid-sized biotech company preparing to distribute a new vaccine to remote regions. Initially, their labeling system relied on generic paper stickers with simple text. However, they soon ran into issues:
- Labels Peeling Off in Refrigerated Trucks: Moisture and cold compromised adhesion.
- Unscannable Barcodes: Ink was smearing or fading over time, leading to scanning failures.
- Difficulty Tracking Shipments: The manual data entry process introduced errors in shipment logs, making recall processes cumbersome.
Partnering with a specialized labeling provider allowed them to re-engineer their approach. They switched to a synthetic label material with an adhesive rated for both cold and humid settings. They also integrated 2D barcodes for more data storage in a smaller space, enabling quick scans. Additionally, a tamper-evident feature helped confirm that no unauthorized party had tampered with the vials en route.
The Result? The biotech firm reduced labeling errors and reported faster throughput in its distribution centers and near-instant recall identification when needed. This streamlined traceability fostered trust among healthcare providers, ultimately contributing to more effective vaccine delivery.
Tips and Best Practices for Implementing Effective Vaccine Labeling
Switching or upgrading your vaccine label solutions might sound daunting, but a few strategic steps can make the process smoother and more cost-effective.
Tip 1: Use an Appropriate Adhesive for Glass Vials
Glass vials require adhesives specifically formulated for non-porous surfaces. Look for labels that mention high initial tack and robust hold under cold conditions. If your vaccines require ultra-low freezers (e.g., -80°C storage), confirm that the adhesive remains functional at these temperatures.
Tip 2: Test Under Real Conditions
Before finalizing a label material, perform controlled tests in the same environment your vaccines will experience. This includes chilling or freezing the vials, applying moisture, and checking if barcodes remain scannable. Early testing often exposes potential issues before they escalate in a live production run.
Tip 3: Incorporate Tamper-Evident Features
Whether you choose a perforated seal or a void-pattern adhesive, tamper-evident features can protect the vaccine’s integrity. Health organizations increasingly expect these safeguards, especially for high-value or high-risk products. Implementing tamper-evident labeling is a small step that can significantly boost security.
Tip 4: Train Your Team
Even the best label design can fail if applied incorrectly. Ensure staff are trained on cleaning vial surfaces before labeling, placing the label in the correct position, and storing labeled vials properly. Also, create a standard operating procedure (SOP) for scanning barcodes to ensure consistent data capture.
If you’re ready to reduce label failures and improve overall sample management, reach out to our team for tailored solutions. We’ll help you select from
Electronic Imaging Materials is your source for expert insights into vaccine labeling solutions. We’ll help you build a system that guarantees clear traceability and reduced operational risks.
Ensuring Long-Term Reliability in Vaccine Distribution
For high-volume or long-term projects, labeling isn’t a one-and-done affair. Environmental changes, frequent handling, and shifting regulatory requirements mean you’ll need a labeling plan that adapts over time. Below are some extended considerations to ensure your vaccine distribution stays consistent and safe.
- Regular Audits: Periodically inspect labels for peeling or fading. If you spot issues, trace them back to root causes—such as storage temperature fluctuations or incomplete surface cleaning.
- Reassessment of Needs: Are you expanding distribution to new regions with different climates? Perhaps you need a label that can withstand hotter, more humid environments. Revisit your label specs regularly as conditions change.
- Software Integrations: Connect barcode data to your ERP or LIMS systems for a holistic overview of inventory and distribution. This can drastically reduce paperwork and manual data entry.
- Supplier Partnership: Work with a supplier who provides ongoing support and can quickly deliver new label batches if your volumes spike or your design changes. Reliability is key in vaccine labeling.
Experience Excellence in Vaccine Labeling With Electronic Imaging Materials
Electronic Imaging Materials (EIM) delivers vaccine label solutions tailored to your unique needs—whether you require tamper-evident seals or cold-storage adhesives. Our team understands the complexities of pharmaceutical labeling and stands ready to help you navigate everything from design to print and application.
- Customized Materials: From glass vial adhesives to specialized coatings, we’ll match you with the right label for extreme conditions.
- Advanced Tech Integration: We’ve pioneered barcode systems that can merge seamlessly with your existing manufacturing processes.
- Dedicated Support: We stay with you every step of the way, offering guidance on label testing, compliance, and ongoing improvements.
Ready to revolutionize your vaccine labeling approach? Reach out and discover how our tailored solutions can elevate your traceability, compliance, and overall efficiency in vaccine distribution.