An organized, safe warehouse is essential for maximum efficiency. However, many warehouses experience problems with their labels failing prematurely or becoming unreadable, which can cause delays and lead to costly errors. If you’re a warehouse manager or anyone in charge of keeping a warehouse running smoothly, understanding why warehouse labels fail can make a huge difference in the daily operations and long-term efficiency of your space.
By understanding the common causes behind warehouse label issues and exploring solutions to these problems, you can establish a reliable warehouse labeling system that endures even in the most demanding conditions. Here’s an in-depth look at what typically causes warehouse labels to fail and some solutions to help prevent these issues.
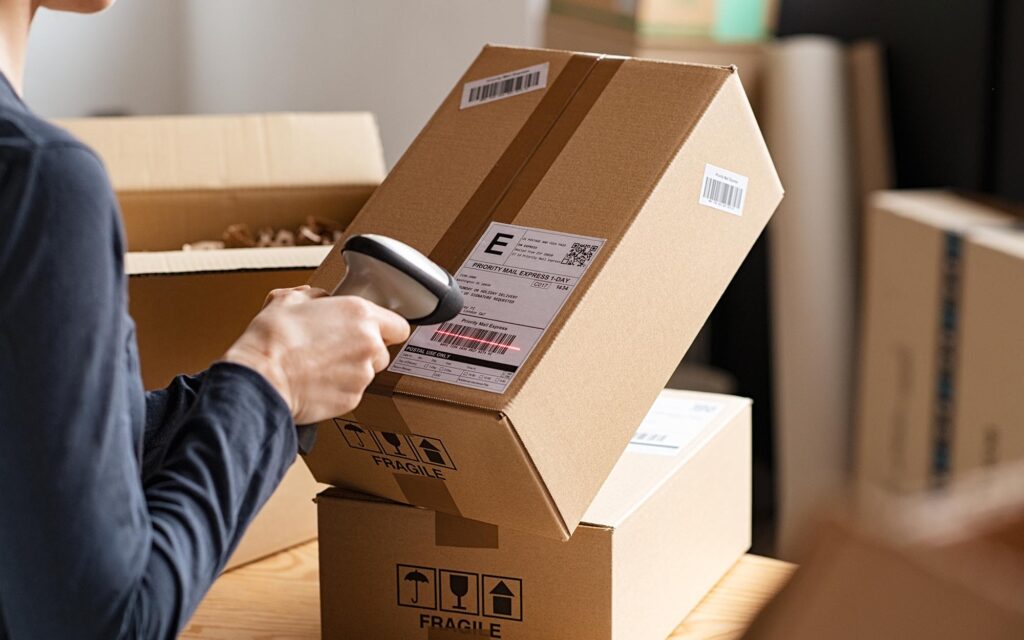
Common Reasons Why Warehouse Labels Fail
There are multiple reasons why warehouse labels often prove unreliable.
1. Environmental Exposure
Many warehouses have fluctuating temperatures, varying humidity levels, and occasional direct sunlight, especially if they include outdoor storage areas. These environmental conditions can cause some types of labels to peel, fade, or lose their adhesive strength over time.
In particular, exposure to direct sunlight or extreme temperatures can weaken the adhesive in many labels. Labels exposed to too much heat may start curling, while cold temperatures can make adhesives brittle, leading to peeling or cracking. Humidity can also be a factor, especially if labels are applied in moist or damp environments, which prevents adhesives from bonding securely.
2. Surface Preparation Problems
Often, labels are applied on surfaces without proper cleaning or preparation. Dust, dirt, oils, and other residues on shelves, bins, or pallets can keep the adhesive from sticking properly. Even a small amount of residue can interfere with the bond, causing labels to peel away quickly or lose readability as grime accumulates.
Warehouse labeling systems require clear surfaces to work effectively. Without proper surface prep, labels can become a frustrating, ongoing problem instead of a reliable solution.
3. Temperatures in the Warehouse
Temperature plays a significant role in the effectiveness of warehouse labels. In facilities with colder areas, like freezers, or sections that get very warm, like those with heavy machinery, labels can fail simply because they weren’t made for those temperatures.
Labels that work fine in moderate temperatures may weaken or fall off in extreme conditions. In cold areas, adhesives might become too rigid to hold; in hot areas, they can soften and slide off.
4. Heavy Floor Traffic and Forklift Wear
Floor labels in warehouses can experience high wear and tear due to the constant traffic from forklifts, carts, and foot traffic. Forklifts, especially, can cause labels to degrade more quickly. When drivers move quickly or turn sharply, they may scrape or run over floor labels, causing damage. Improperly trained drivers can add to this problem, as they may accidentally drag forklift forks, scraping and tearing the labels.
Heavy traffic alone can lead to significant wear and tear on floor labels. Over time, labels can become unreadable or peel away entirely due to scratches, scrapes, and other physical impacts. Additionally, small bits of debris dragged by wheels can grind against labels, leading to premature failure.
Jay C. | ForestOne
“The streamline shields are a very unique way of labeling floor tags. Our company really liked them. I am trying to introduce them to our other branches nationwide across Australia.“
5. Contamination and Chemical Spills
Warehouses that handle chemicals or have frequent spills may find that these substances break down the adhesives or materials used in warehouse labels. For example, floor cleaners, oils, or certain industrial chemicals can dissolve adhesives, making labels unusable in a matter of hours. This issue is especially common in warehouses where regular cleaning solutions and chemicals are used to maintain safety and cleanliness.
6. Incorrect Label Material
Not all warehouse labels are created equal, and using the wrong type of label material can lead to frequent problems. For example, labels made with standard paper or low-quality plastics are often insufficient for heavy-duty applications. For metal surfaces, certain materials adhere better, while others fall off quickly. Choosing the correct adhesive and material combination is crucial; otherwise, labels may fail due to material incompatibility.
Additionally, using incorrect metals in label plates, like mild steel when stainless steel is needed, can result in corrosion or rapid wear in high-moisture environments. Similarly, lightweight plastic labels can crack and fail in high-impact areas, while stronger metals like aluminum or steel might be more effective.
Discovering the composition of your label materials can be a mystery, but we’re here to help decipher it! From paper to vinyl to polyester, each material has unique qualities for different applications.
Practical Solutions to Prevent Warehouse Label Failures
Understanding why warehouse labels fail is the first step. Next comes finding effective solutions to these issues. Here’s how to address these common problems to create a reliable and efficient warehouse labeling system.
Step #1: Choose Labels Designed for Environmental Conditions
Opt for durable warehouse labels that are made for specific environmental factors. In warehouses with high temperatures, select heat-resistant labels, and in cold storage areas, look for labels with cold-friendly adhesives. Moisture-resistant labels are ideal for areas with high humidity or occasional spills. In outdoor storage sections, UV-resistant labels will last longer by reducing sun damage and fading.
Step #2: Proper Surface Preparation for Label Application
Taking the time to properly clean and prepare surfaces before applying labels can prevent peeling and ensure strong adhesion. Make sure surfaces are free from dust, dirt, oils, and moisture by wiping them down with a clean, dry cloth. For more difficult residue, an alcohol wipe can help clear contaminants that prevent adhesion.
By consistently cleaning surfaces before applying labels, you’ll extend the lifespan of each label and reduce the frequency of reapplication.
Step #3: Match Label Materials to Temperatures
When dealing with temperature extremes, ensure your labels and adhesives are rated for those temperatures. Labels made for cold storage or freezer environments use special adhesives that stay flexible even at low temperatures, while high-temperature-resistant labels have adhesives that don’t soften or melt in the heat.
Step #4: Use Durable Floor Labels for Heavy Traffic
Choose heavy-duty floor labels designed to withstand regular forklift and cart traffic. Some barcode labels for floors are made with high-durability laminates or protective layers that resist scratching and impact damage. Others are designed with raised edges or recessed designs that allow the wheels of carts and forklifts to pass over without direct contact, significantly reducing wear and tear.
Floor label durability can be increased by ensuring that forklift operators are trained to avoid driving erratically over labels whenever possible. Keeping traffic areas clean and clear of debris also helps prevent floor label wear.
Step #5: Opt for Chemical-Resistant Labels for Certain Areas
For warehouses that handle or store chemicals, chemical-resistant labels are essential. These labels are made from materials that resist solvents, oils, and other chemicals, ensuring that they won’t break down or peel when exposed.
Additionally, plan label placement carefully to avoid high-spill zones or areas frequently cleaned with strong solvents. For added protection, some warehouses apply an extra clear laminate over labels to provide a barrier against spills and scrapes.
Step #6: Use the Correct Label Material for Specific Needs
Selecting the right label materials can prevent a range of issues. For instance, heavy-duty plastic labels or metal plates may be ideal for high-impact areas, while simple adhesive paper labels might suffice in low-touch areas. In warehouses with metal surfaces, use magnetic labels or those with adhesives designed to work well with metals like aluminum or stainless steel.
Understanding the strengths of different types of labels can guide you in selecting materials that won’t fail under specific conditions. Additionally, incorporating barcode labels into your system can improve tracking and organization. By pairing the right label type with the right material, you can create a labeling system that works well across various warehouse settings.
Key Takeaways: How to Improve Warehouse Operations with Better Labeling
- Warehouse labels may seem like a small detail, but they play a huge role in overall efficiency. With a well-thought-out warehouse labeling system, you’ll avoid frequent reapplications and reduce the frustration of dealing with peeling, fading, or damaged labels.
- The right labels, combined with proper preparation and maintenance, will help you create an organized, efficient, and safe warehouse environment.
- Taking the time to understand the specific needs of your warehouse and using the correct types of labels can save both time and money.
Achieve Unstoppable Efficiency with EIM’s Durable, Reliable Warehouse Labels!
Tired of dealing with peeling, faded labels? Connect with EIM today to explore tough, customized warehouse labels that stand up to any challenge. Enhance your operations with labels built for lasting visibility and strength—request a free sample now!