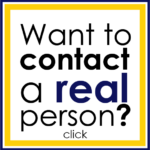
So, you’ve graduated to the big leagues ―to the pinnacle of label printing―into the world of thermal transfer printing? Your laboratory labeling challenges have exceeded the capabilities of the lowly laser printer and even the constrictions of direct thermal printing, eh?
You need really durable labels—these other technologies will simply not do the job.
While you totally get the strengths and specifications of a thermal transfer printer, you may be at sea about the ribbon thing. Let’s start with a little primer:
Thermal Transfer Printing Ribbon
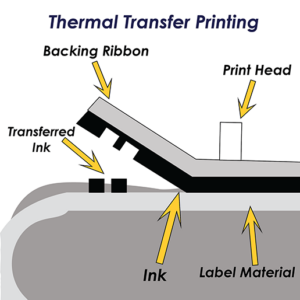
A thermal transfer printer prints on a substrate (such as paper or some other material) by melting a coating of ribbon so that it stays glued to the material. Thermal ribbons come in roll form with three main formula choices—Wax, Wax/Resin or Full Resin. The ink formulas are coated on one side of a thin polyester backing and wound either “face in” or “face out” depending on your printer’s specifications. This means that the coating side (aka the side that meets the label) is either on the inside or the outside of the roll. When heat is applied from the print head, it makes the ink release from the backing sheet or carrier and stick to the label or tag.
The three ink categories cover all the basic needs of thermal transfer printing—either on paper, on mid-range plastics or on glossy, hard films (such as polyester). Due to the wide array of label and tag materials, the extensive number of printers being used, and the endless types of tube, vial, slide and plate applications to which lab labels are subjected, ribbon manufacturers have developed a broad selection of ink formulas within each category. You get some of the best print durability with thermal transfer technology because the bond created between a well-matched ribbon and its label partner can be far superior to other ink technologies. You can often avoid the need for a protective film laminate, which creates not only an additional cost consideration but may not fit your printing on-demand needs. EIM offers ribbon/label combinations that are fully tested to work well together in all types of laboratory and healthcare applications.
WAX RIBBONS are typically for printing on matte or semi-gloss paper labels used on tubes and patient files. Here the labels can survive without smudging for many years. However, the labels should be kept dry, and must not be abraded or subjected to chemicals/oil—all of which could melt the wax image.
WAX/RESIN RIBBONS are specially blended to produce a finer image on papers and many synthetic films. You can get more scratch, abrasion and moisture resistance than with wax ribbons. In fact, some wax/resin formulas―well-matched to specific label materials―even offer chemical resistance. Since many labs require durable, yet flexible labels (typically made of polypropylene and other polyolefins ), wax/resin ribbons are very popular.
RESIN RIBBONS are formulated to print on all types of plastic labels—such as polyester, polypropylene and vinyl. The ink is designed to slightly dissolve into the plastic surface of the label and with a tight adhesion to the label, the label then becomes extremely durable. Plastic labels with resin printing will survive immersion in water, are highly scratch-resistant and can be resistant to chemicals, solvents and oils (depending on the specific resin formula). When you need to meet the challenge of demanding lab conditions—such as chemical-resistant identification or cryogenic storage—a super-durable resin ribbon will be the clear choice.
The choice of what thermal transfer printing ribbon to use depends on your lab’s needs and investment dollars.
If a multiple-choice quiz always throws you into a panic, call us at 800.535.6987. When in doubt, shout! (If you prefer, you can always email us: LabelExperts@eiminc.com or fill out this form.) We’ll calm you down and get you on the right track.