You’re in the middle of an experiment when you realize you can’t read the labels on several frozen tubes. Maybe they’re peeling off, fading, or smudged beyond recognition. What now? Fumbling to relabel or identify mystery samples can derail workflows, increase costs, and undermine research accuracy. When working in cold-storage environments—especially cryogenic ones—labeling failures aren’t just inconvenient; they can compromise valuable data or jeopardize compliance protocols.
In this post, we’ll walk through the common issues with frozen tube labels, explaining exactly why they fail and how you can protect your lab against these pitfalls. From the nuances of choosing the right adhesive to the importance of correct printing techniques, we’ll reveal every detail you need to prevent label failure in cryogenic storage.
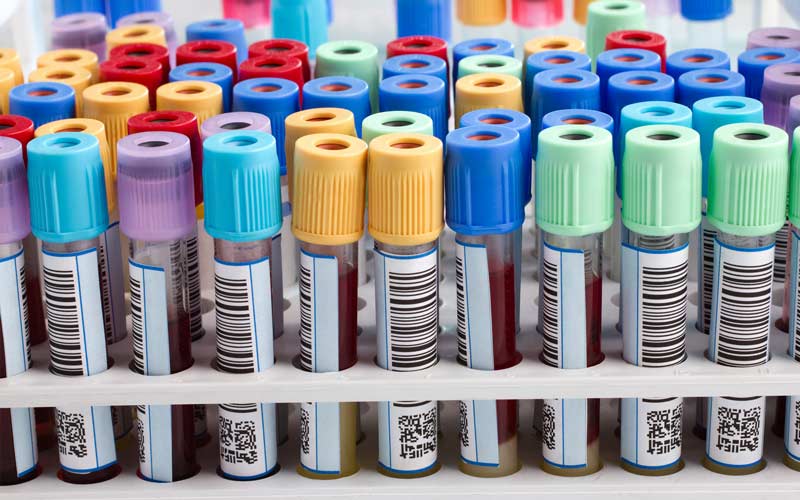
Why Do Frozen Tube Labels Fail Under Extreme Conditions?
Extreme cold wreaks havoc on ordinary labels. When temperatures plunge below freezing—sometimes as low as -196°C in liquid nitrogen—the materials and adhesives that work fine at room temperature suddenly face a world of stress. Frozen surfaces can accumulate frost or condensation, further weakening label adhesion. And that’s just the start. Freeze-thaw cycles, chemical contact, and friction in busy lab settings can all contribute to label degradation.
Understanding these stressors is the first step toward preventing label failure. Once you grasp what your labels are up against, you can take specific measures to ensure they remain intact and readable. Below, we outline the top five culprits behind frozen tube label failures, followed by actionable steps you can take to protect your samples and data.
1. Adhesive Issues
One of the most pervasive common issues with frozen tube labels is adhesive failure. When you stick a label onto a frozen tube, any frost or moisture on the tube’s surface can limit how well the adhesive bonds. Similarly, adhesives designed for room temperature may become brittle or lose tackiness at very low temperatures.
Why It Matters
- Risk of Peeling: Labels that peel off in storage can easily become lost or swapped, causing confusion and potential sample mix-ups.
- Reduced Readability: Even if the label stays partially adhered, edges may lift or curl, making it harder to scan or read critical details.
- Costly Downtime: Constantly re-labeling tubes wastes time and resources and disrupts workflow.
How to Prevent It
- Choose Cryo-Grade Adhesive: Look specifically for adhesives rated for cryogenic temperatures. These are formulated to remain sticky in sub-zero conditions.
- Choose Wisely: Purchase labels made to adhere to pre-frozen tubes.
- Press Firmly & Evenly When Applying: To promote better contact, apply even pressure across the entire label surface.
2. Material Problems With Cryogenic Labels
Selecting the wrong label material is another major reason tubes lose their labels in frozen environments. Standard paper labels might be fine for short-term room-temperature storage, but they simply can’t withstand liquid nitrogen or ultra-cold freezers.
Cryogenic Labels Are Built for the Cold
Cryogenic labels often feature synthetic materials like polyester or polypropylene. These materials remain flexible when cold and resist tearing or cracking, making them ideal for handling extremely low temperatures and repeated freeze-thaw cycles.
What to Look For in Durable Labels
- Moisture Resistance: Freezing can create condensation, which weakens paper labels. Synthetic materials that repel water are key.
- Chemical Tolerance: Some labs use solvents or disinfectants on tubes. A label that dissolves upon contact with certain chemicals will quickly become unreadable.
- Strong Adhesive Backing: The best cryogenic labels include adhesives designed to bind with synthetic materials under cold conditions.
Don’t forget: durability also involves the ability to maintain a clear print. Even if the label remains stuck, smudged text or blurred barcodes can be just as detrimental as a missing label.
Danielle H. | Nikkiso Cryo, Inc.
“Our label challenges have been resolved since ordering with EIM.“
3. Printing Errors
When you’re preventing label failure, it’s easy to focus on adhesives and materials while overlooking the importance of your printing method. Whether you’re printing barcodes, alphanumeric text, or color codes, the ink or printing ribbon you choose can make or break label longevity.
Common Printing Pitfalls
- Incompatible Inks: Certain inks aren’t designed for cold conditions and may bleed or fade when frozen.
- Poor Ribbon-Label Match: If you use thermal transfer printing, your ribbon material should match the label’s topcoat to ensure the image bonds effectively.
- Inconsistent Heat Settings: In thermal transfer systems, the wrong heat setting can produce faint or incomplete prints.
Tips for Better Printing
- Use High-Quality Ribbons: Opt for resin-based ribbons if you need strong resistance against chemicals and extreme temperatures.
- Optimize Printer Settings: Refer to the label manufacturer’s instructions for recommended printer heat and speed settings.
- Test Before Batch Printing: Do a small run first to ensure text and barcodes look sharp and remain intact after freezing.
4. Application Mistakes
No matter how advanced your label material or adhesive, improper application can lead to immediate failure. If the tube surface is dirty, wet, already cold enough to have formed frost or has a label material engineered to adhere to frosted surfaces, your label has little chance of fully adhering.
Common Mistakes
- Labeling Wet Surfaces: Moisture under the label acts as a barrier between adhesive and tube, leading to poor adhesion.
- Touching the Adhesive: Fingertips can leave oils that hinder the label’s ability to stick.
- Applying Labels in a Rush: Misaligned labels can bubble or crease, leaving gaps for air and moisture.
Best Practices
- Clean & Dry Tubes: Even a quick wipe with an alcohol pad can remove oils or residue. Let the surface dry fully before labeling.
- Handle Labels with Care: Try not to touch the adhesive side; consider wearing gloves to minimize contamination.
- Apply Firm Pressure: Smooth out any bubbles and firmly press around the tube’s curvature to ensure maximum contact.
Putting in the extra effort during label application can make a world of difference in preventing label failure, especially when you’re dealing with precious samples.
5. Incompatibility With Equipment
Many labs rely on barcodes or RFID (Radio-Frequency Identification) to track samples in cold storage. But if these technologies aren’t compatible with your scanning equipment—or if the label design doesn’t match your reader’s capabilities—then you’ve got a recipe for frustration.
Potential Equipment Conflicts
- Barcode Readers Struggling with Low Contrast: If your frozen label frosts over or if the print fades, a standard barcode scanner may not recognize it.
- RFID Tag Interference: Metal racks or crowded freezer environments can block RFID signals.
- Data Handling Errors: If the system encoding doesn’t match your lab’s data fields, you might run into confusion when scanning.
How to Mitigate Tech Issues
- Check Compatibility: Confirm that your scanner supports your label’s barcode type (1D, 2D, etc.) or RFID frequency.
- Trial Runs: Test sample tubes in real-world conditions to see if barcodes remain scannable after freezing.
Robust Data Management: Make sure your lab’s software or LIMS (Laboratory Information Management System) aligns with the data encoded on labels.
If you’re tired of peeling labels, smudged text, or barcodes that just won’t scan, reach out to Electronic Imaging Materials for guidance. We specialize in creating durable labels that stand up to cryogenic storage, repeated freeze-thaw cycles, and even harsh chemicals.
Choosing the Best Labels for Cryogenic Storage
If you want to establish a failsafe labeling strategy for your frozen tubes, start by selecting the right label materials and adhesives. Cryogenic labels are engineered to withstand the most punishing conditions—think -196°C in liquid nitrogen or repeated freeze-thaw cycles. But how do you sift through the options?
Here are a few key factors to consider:
- Adhesive Rating: Ensure the label explicitly states it’s cryogenic-rated. This typically means it’s tested to remain functional at ultra-low temperatures.
- Material Composition: Look for synthetic materials like polyester or polypropylene, which handle cold, moisture, and friction better than standard paper.
- Printer Compatibility: Make sure the labels work with your printer type—thermal transfer, direct thermal, or otherwise.
- Surface Design: If you need extra defense against solvents or repeated handling, consider labels with wrap-around features or protective laminates.
What Steps Can Prevent Labeling Failures in Freezing Applications?
Once you’ve identified the right label materials, adhesives, and printer settings, the next step is fine-tuning your process. It’s easy to skip a step here or there, especially when you’re juggling multiple lab duties, but consistency is key.
Here’s what you should do:
- Inspect Tubes Pre-Labeling: Look for cracks, residual frost, or any surface damage that might hinder label adhesion.
- Wipe Down Surfaces: Ensure tubes are dry and free of oil, dirt, or leftover adhesives from previous labels.
- Choose the Right Time to Apply: To reduce condensation, apply labels at room temperature or in a controlled environment.
- Press and Seal: Use firm, even pressure across the entire label. Avoid bubbles or creases.
- Allow Adhesion to Set: Some labels recommend a brief “cure” time before exposing them to extreme cold.
- Verify Readability: Scan barcodes or check for smudging before placing tubes into storage.
Partner With Electronic Imaging Materials for Dependable Labeling
We’re committed to helping labs like yours conquer the toughest labeling challenges. Whether it’s ultra-cold freezers, routine freeze-thaw cycles, or chemical exposures, our solutions are designed with one overarching goal: preventing label failure. We understand how important it is to maintain sample integrity and compliance, so we customize our labels and adhesives to suit your exact requirements.
Ready to secure your lab’s future against mislabeled or unidentifiable samples? Get in touch with our team and discover how EIM can enhance your labeling process, saving you time, money, and unnecessary complications in the long run.