Would you use gas-receipt paper to keep your important information? You know the stuff: Very thin, flimsy paper that gas pumps, slot machines, cash registers and information kiosks spit out after each transaction. If you don’t crumple it up in a little ball right away, you may tuck it away for an expense report or taxes. But you would never expect it to hold up to moisture, chemicals or oily surfaces. Wouldn’t be prudent. Isn’t going to happen.
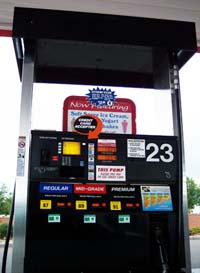
This kind of material is printed by a thermal technology—or more accurately called Direct Thermal (DT) printing. A direct thermal printer produces a printed image by passing specially-treated thermochromic (a fancy word for heat-activated) paper over a print head (that’s the thingy that actually transfers the image). The coating on the thermal paper turns black in the areas where it is heated, producing the image. The benefit to this type of printing is that it’s fast, inexpensive and requires no consumable media other than the paper. As a consequence, the cost per label is lower. The disadvantage is that the image degrades over time, so direct thermal (DT) labels are primarily used for short-term use. DT labels will fade or brown with age and will even turn black if exposed to heat or strong sunlight. (Ask any disappointed mother who wanted to keep her baby’s sonogram image in a baby book forever!)
The biggest disadvantage lies in the limited number of materials suitable for direct thermal printing. There’s paper, of course, for general-purpose applications. And there’s a finite number of plastic materials—which offer better durability than paper and some resistance to abrasion, moisture and chemicals. [Emphasis on the word some.] This is ideal for, say, laboratory facilities that need quality printed labels that can resist harsh chemicals and yet are economical enough to be thrown away after short-term usage.
A more durable and versatile type of printing is known as Thermal Transfer (TT) technology. Thermal transfer printing is a method that uses a heat-sensitive ink ribbon instead of a heat-sensitive paper. A TT printer has a print head containing many small resistive heating pins that—upon contact—melt a wax-based ink or resin-based ink onto the stock. Thermal transfer is preferred over direct thermal printing on surfaces that are heat sensitive or when long-term higher durability of printed matter (especially against heat or sunlight) is required.
Thermal transfer is typically the print method of choice. Why? For one thing, there are so many choices for the end-user (that’s you) in terms of thermal transfer face stock, adhesives, topcoats, liners, over laminates and printing ribbons. In fact, almost an infinite number of permutations in this cornucopia of thermal transfer options:
Materials: Some TT products exhibit excellent resistance to water, smudging or tearing. Others withstand alcohol, methanol, oils and other chemicals. Some are suitable for food contact and are grease resistant. Other materials are engineered to conform to irregular shapes and tight diameters. Certain fragile materials are perfect for security applications due to their destructible features. There are TT materials that survive -40°F blast freezing, -80°F cryogenic temperatures and even extreme-heat conditions up to 1000°F. Then there’s RoHS compliant, UL-Recognized, FDA or MIL Standards approved. There’s archival quality paper that is acid- and lignin-free. Dazzling, huh?
Topcoats: Made to refine your print quality, they can be easily added to the base material (aka stock) and come in gloss, semi-gloss, matte and frosted finishes as UV-screen, water-screen, solvent-screen, water-based, and solvent-based.
Adhesives: The choices here are practically endless, too. Removable, temporary, repositionable, aggressive, super-aggressive, high-performance, general-purpose, tamper evident (with words like “VOID” or a checkerboard pattern), acrylic, rubber-based, silicone, cryogenic or frost-resistant, high-temperature, quick tack, shrink resistant, water and humidity-resistant, and solvent-resistant. Some bond to rough, high-textured substrates, oily or greasy surfaces and low-energy surfaces. Others come off as easily as Post-It® Notes.
Over Laminates: Available in different thicknesses and some even have texture, these clear films add a glossy, matte or frosty finish to your labels at the same time providing extra protection against moisture, chemicals, solvents, abrasion and UV light.