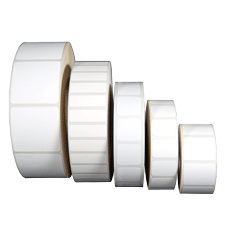
“We don’t only care about quality when mistakes are made. We work to continually evaluate our processes so we can improve our labels. We take quality seriously all the time.” – Quality Coordinator Cecilia Robinson
Our initial obsession with quality started with EIM’s founder, Paul Henkel. Paul wanted to make his new business stand out from other label manufacturers. He also needed to figure out how to prevent labels getting damaged during delivery, a repeat problem for our customers.
For starters, Paul elected to start shipping with thicker, more durable cardboard boxes. It helped protect labels from damage, but still wasn’t the level of shipping quality Paul was aiming for.
Paul came up with the idea of placing rolls of labels on cardboard cores and stabilizing those with a custom designed cardboard grid. Instead of receiving a tossed about pile of label rolls, a customer would open a neatly organized box with their product in pristine condition. It took a couple years to iterate the best combination of box sizes and internal packaging, but Paul’s custom packaging system is still used today, ensuring EIM’s labels arrive safely at your door.
Label Quality: Every Department Matters
At EIM, your labels go through almost every department on their way out the door to you. Once your order is confirmed, it goes through multiple quality checkpoints before it travels from our doorstep to yours.
- A Sales Account Manager or Customer Service Rep will talk through your order to verify we’re sending the correct type of label.
- Our PrePress department then double checks barcode data files and label design before sending the final proof to you.
- PrePress also handles our #1 quality issue that comes up for customers: artwork quality. Luckily, our PrePress department consists of talented graphic designers. They’re quick to catch artwork related issues and help customers fix them!
- Our Purchasing Coordinator examines every order to make sure all the supplies needed to make it are in stock.
- Once your label order gets to the Production floor it goes thru a series of checkpoints before, during, and after printing. Machine Operators will first verify their printer is correctly set up. Other Production employees will swing by to double check labels before printing commences, and cross check them once the order is completed.
- As you know from our opening story, our Shipping department takes the packaging of your quality labels very seriously. They’re also our last quality checkpoint and have caught missed mistakes in the nick of time!
But What Happens If My Labels Are Wrong?
But what about a worst-case scenario where a quality issue slips by undetected? We always want to help a customer with a messed-up order put things right. This is where Quality Coordinator Cecilia Robinson steps in.
“We want customers to have labels in hand as soon as possible if they’ve received incorrect labels. Especially if this has caused any sort of delay on our customer’s end,” Cecilia says. “We start by finding the root cause to avoid the same error happening on the customer’s replacements. Then we move forward with making replacements as soon as we possibly can.”
Label Quality Questions? Reach Out!
Questions about label quality or quality related issues like ISO or UL compliance? Email us!