You’ve just designed the perfect label for your latest medical device—clear symbols, compliant text, and a scannable barcode. But when it comes time to apply the label, it won’t stick properly to the device’s surface. Or worse, it peels off after sterilization, risking serious compliance failures and potential harm to patients. Choosing the right adhesive for medical device labels is more than a finishing touch; it’s a factor for long-term safety, traceability, and regulatory compliance. This guide will walk you through the key considerations so you can confidently select an adhesive solution that won’t let you—or your labels—down.
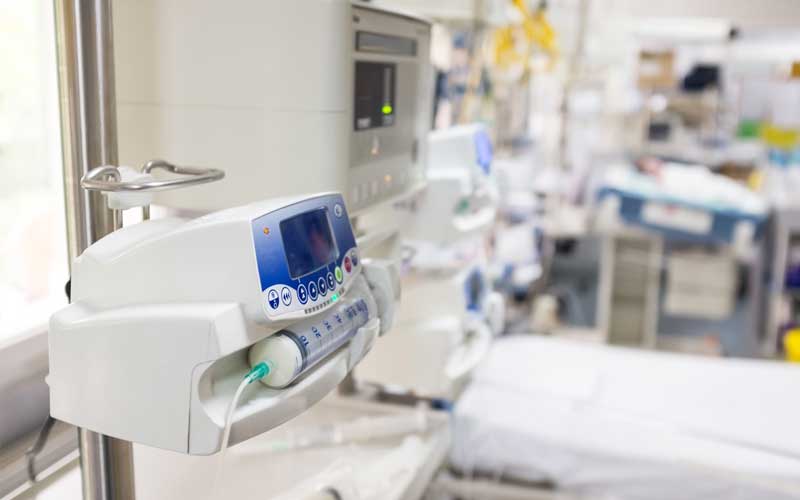
Why Adhesive Selection Matters for Medical Device Labels
When we talk about medical device labels, it’s easy to focus on text clarity, symbols, and regulatory markings. However, even the most perfectly designed label becomes useless if it can’t stay attached. In a hospital or laboratory environment, devices often face repeated sterilization, heavy chemical exposure, and daily wear and tear. If the label peels or fails mid-use, it compromises compliance and could create safety risks. Some potential consequences include:
- Regulatory Scrutiny: Agencies like the FDA or EU MDR expect labels to remain legible and secure throughout a device’s lifecycle.
- Patient Harm: Missing warnings or instructions can lead to improper use.
- Tracking Failures: Barcodes must remain intact for traceability and recall efficiency.
- Damage to Brand Reputation: Healthcare providers rely on consistently readable and durable labeling. Frequent label failures erode trust.
Key Factors to Consider When Choosing an Adhesive
Choosing the right adhesive for medical device labels requires careful consideration of multiple factors, including material compatibility, environmental exposure, regulatory compliance, and the need for durability or removability.
Surface Material Compatibility
Medical devices come in many forms: injection pens with curved plastic surfaces, surgical instruments made from stainless steel, or glass-based diagnostic tools. Each substrate has unique surface energy and texture, directly influencing how well an adhesive bonds. For instance:
- Low-Surface Energy Plastics (e.g., Polyethylene, Polypropylene): Require adhesives specifically formulated to create a strong bond on slick or oily surfaces.
- Metals (e.g., Stainless Steel, Aluminum): Generally higher surface energy, but may face repeated sterilization.
- Glass: Often needs adhesives that won’t break down with chemical sanitizers or autoclaving.
Environmental & Sterilization Resistance
From high-heat autoclaves to chemical exposure in operating rooms, the environment your device encounters shapes adhesive needs:
- Heat & Moisture: Adhesives can degrade in high-temperature, high-humidity settings.
- Chemical Solvents & Disinfectants: Alcohols or potent cleaning agents can weaken certain adhesive bonds.
- Repeated Sterilization: Ethylene oxide, gamma radiation, or steam autoclaving can degrade labels if they aren’t designed for such processes.
Regulatory Compliance
Medical device labeling must meet stringent requirements under FDA regulations, EU MDR, ISO 10993, and more. These standards often specify how labels should perform under certain conditions and may require biocompatibility assessments to ensure no harmful chemicals leach from the adhesive.
Durability & Removability
Some medical device labels need to stay on permanently, enduring the entire lifespan of an implant or instrument. Others require easy removal for reprocessing or recalibration. Knowing whether you need a permanent or removable adhesive will guide your choice:
- Permanent Adhesives: For devices where the label must remain intact indefinitely—no residue, no peeling.
- Removable Adhesives: For labels that must be peeled off cleanly without damaging the device or leaving adhesive behind.
Marco F. | Strados Labs
“They were able to provide us with a high-performance customized solution for our medical device in a very short amount of time during the busy season.“
Types of Adhesives for Medical Device Labels
Different types of adhesives offer varying levels of durability, chemical resistance, and bonding strength, making it essential to select the right formulation based on the specific needs of your medical device application.
- Acrylic Adhesives: Known for excellent chemical and temperature resistance, making them a top choice for healthcare settings. They bond strongly to a variety of surfaces but can be slower to set.
- Rubber-Based Adhesives: Offer quick tack and strong initial bonds, but often less resistant to heat and chemicals compared to acrylics.
- Silicone Adhesives: Ideal for sticking to low-surface energy substrates and remain stable in high temperatures, but can be costlier.
- UV-Curable Adhesives: Hardens rapidly under UV light, providing a durable bond. Often used in specialized manufacturing processes.
Testing Adhesives for Optimal Performance
Even if an adhesive’s datasheet claims compatibility with specific materials or sterilization methods, real-world testing is critical. Environmental factors, manufacturing processes, and unique device features can all affect label adherence. Here are some recommended steps:
- Surface Preparation: Make sure the device is clean and free of oils or residues that can degrade adhesion.
- Application Testing: Apply labels on sample devices and expose them to actual or simulated sterilization cycles (e.g., autoclave, chemical disinfectants).
- Aging Studies: Evaluate how well labels hold up after weeks or months of storage, especially under humidity or temperature extremes.
Electronic Imaging Materials offers guidance on adhesive selection. We’ll help you identify the perfect match for your material, environment, and compliance requirements so your labels remain intact from production all the way through patient use.
Adhesives That Protect Patients and Brands
The adhesive might be the last thing you think about when designing a label—but it can be the first point of failure if it’s not up to par. A suboptimal bond can result in compromised compliance, potential patient harm, or lost data. On the other hand, selecting the right adhesive paves the way for safe, efficient, and fully trackable medical device labels that meet the rigorous demands of modern healthcare.
- Match Surface & Environment: Pick adhesives that are chemically aligned with your device’s substrate and any sterilization processes.
- Plan for Regulations: Ensure your adhesive meets key standards like ISO 10993 for biocompatibility and aligns with FDA or EU MDR guidelines.
- Test Thoroughly: Simulation of real-world conditions, from extreme temperatures to repeated handling, reveals potential pitfalls early.
Where Adhesive Expertise Meets Regulatory Know-How
Electronic Imaging Materials helps manufacturers overcome the challenges of medical device labels. Our team understands that everything—from adhesive chemistry to barcode design—must align with healthcare environments and compliance standards. Whether you’re struggling with sterilization issues, facing tough surfaces, or needing specialized laminates, we have the know-how to guide you.
- Custom Solutions: We tailor adhesives and label constructions to your exact application—no one-size-fits-all approach here.
- Robust Testing Protocols: Our labels undergo rigorous evaluations for heat, chemicals, and mechanical stress to guarantee long-lasting performance.
- Regulatory Alignment: From FDA and EU MDR to ISO 10993, our solutions help you check all the boxes for safe, compliant labeling.
Ready to secure your labeling process from end to end? Reach out and discover how the right adhesive can elevate your medical device labeling—and your brand’s reputation—in one seamless step.