One label doesn’t fit all. The label needs to do more than stick, especially when it comes to single and multi-use devices. It must support compliance, safety, and performance across different lifecycles.
Labeling ensures patient safety, regulatory compliance, and product integrity. And yet, many teams overlook the distinct labeling needs of single-use versus multi-use products.
This article breaks down the differences, highlights key material and design considerations, and guides you toward smarter single-use device labels and multi-use options tailored to your products.
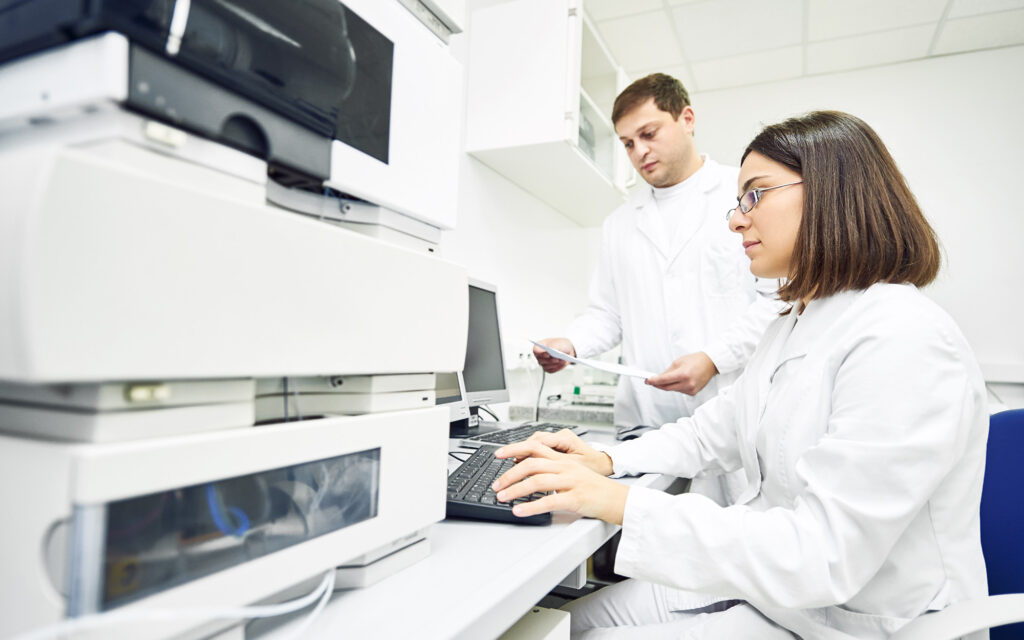
How Labeling Requirements Differ by Device Lifecycle
Understanding the intended use of a medical device is the foundation of effective labeling. Single-use and multi-use devices face vastly different environmental conditions. That difference shapes the labels needed to support them.
Single-use device labels are disposable, designed to be used once and discarded. The labeling requirements are generally less intense. Labels need to survive packaging, transit, and brief clinical use.
Multi-use devices are built for repeat use. This means they must undergo sterilization, disinfection, and rigorous handling. The label attached to a reusable medical device has to withstand these stressors without degrading.
This difference in lifecycle demands two very different labeling strategies.
Single-Use Devices Are Simpler, But Still Regulated
Single-use medical devices, such as syringes, catheters, or diagnostic swabs, are designed for one application and immediate disposal. Their labels must deliver short-term performance, but are no less important for compliance.
Single-use device labels must remain intact through shipping, storage, and clinical handling. While exposure to moisture or abrasion is limited, accuracy and readability still matter. Details such as lot numbers, expiration dates, and UDI information must be visible.
Material choices are often more economical: paper-based or basic synthetic labels paired with standard pressure-sensitive adhesives. Direct thermal or thermal transfer printing is common, provided it meets legibility standards.
Multi-Use Devices Are Built for Reprocessing, Demanding Durable Labels
Unlike disposables, multi-use devices go through repeated reprocessing cycles—sterilization, cleaning, disinfection, and more. Think surgical instruments, endoscopes, or reusable monitors.
These labels need serious staying power. They face high heat, chemical exposure, moisture, abrasion, and frequent handling. Labels that smear, lift, or degrade can interrupt traceability and open the door to compliance issues.
That’s why labels for multi-use devices must be made from high-durability synthetics like polyester. These materials, paired with strong adhesives and topcoats, can resist autoclaving, EtO, gamma radiation, and harsh solvents.
Durability and Traceability Requirements
Traceability is essential for both single-use and multi-use devices, but the standards and durability needs differ significantly.
Single-Use Devices
They usually need batch-level identification. Single-use device labels must include scannable barcodes or human-readable information that remains intact through manufacturing, shipping, and short-term clinical use. Because these devices are disposed of after one use, the label’s durability window is relatively short, but it still must meet compliance standards.
Multi-Use Devices
Multi-use devices often require a unique identifier for each item. This label may be permanently affixed to the device itself to ensure full lifecycle traceability. Labels must remain intact and readable even after exposure to cleaning agents, sterilization processes, and repeat handling. These labels support UDI compliance while also enabling maintenance records and usage tracking across multiple use cycles.
Adhesive Considerations by Use Type
The adhesive is the unsung hero of medical device labeling. Its role changes significantly depending on whether the label is intended for a single-use or a multi-use product. These differing use cases shape how an adhesive must perform to ensure label survival and regulatory success.
Adhesive Performance in Single-Use Devices
For single-use device labels, adhesives need to form a strong bond with materials like foil pouches or plastic wraps. These labels don’t face extreme environments, but they still need to stay in place through packaging, shipping, and clinical use.
Adhesive Demands for Multi-Use Devices
Multi-use devices require adhesives that go beyond basic bonding. They must endure repeated exposure to steam, disinfectants, and physical handling. This isn’t just a sticker. It’s a high-performance adhesive system designed for the medical field.
Adhesive Demands for Multi-Use Devices
Choosing the right adhesive involves more than a quick compatibility check. You need to account for the device substrate, sterilization method, and surface texture. A label that looks great on paper won’t last five minutes in an autoclave if the adhesive isn’t engineered for it.
Whether you manufacture single-use products or design complex multi-use systems, the wrong label can cost you. Electronic Imaging Materials helps device manufacturers select label systems engineered for your specific lifecycle, materials, and compliance needs.
Regulatory Differences and Compliance Pressures
While both single-use and multi-use device labels must meet FDA and international regulatory standards, the specific requirements and pressure points vary in important ways. Understanding those distinctions is key to choosing the right labeling approach and avoiding costly missteps.
For Single-Use Devices
- Labels are typically applied to the device’s packaging rather than the device itself. These labels must present all the required information clearly and legibly.
- UDI (Unique Device Identification) compliance usually focuses on the outer packaging and must remain intact and scannable until the product is used.
- Even though the device is discarded after use, the label still plays a vital role in traceability and must remain readable through handling and clinical use.
For Multi-Use Devices
- UDI markings may need to be applied directly to the device, not just the packaging, because the label must persist across multiple uses and reprocessing events.
- These labels must withstand sterilization methods such as autoclaving, EtO, and chemical disinfection without fading, peeling, or degrading.
- Additional labeling content may be required, including instructions for reprocessing, warnings, or maintenance logs that are visible and durable for the life of the device.
Sterilization Impact on Labels
One of the biggest stressors on medical device labels is sterilization. Sterilization’s impact on labels can lead to fading ink, peeling edges, or full label failure. For multi-use devices, selecting label materials and adhesives that hold up under autoclaving, EtO gas, and other sterilization methods is crucial. Even single-use packaging may face some sterilization steps before distribution, requiring careful material selection.
The stakes are high. Failing to meet these regulatory details can result in compliance violations, recalls, or worse. Choosing the right label ensures you stay aligned with regulations and focused on patient safety.
Best Practices for Optimizing Label Performance
No matter which category your device falls into, following these best practices can significantly reduce labeling risks and enhance overall performance:
- Choose materials based on the actual environment they’ll face. Prioritize durability in the face of heat, chemicals, or moisture, not just price.
- Pay close attention to adhesives. They are vital to maintaining label integrity, especially under stress from sterilization or handling.
- Validate durability under realistic conditions. Simulated cleaning and sterilization cycles can reveal weaknesses before they reach the field.
- Make sure all barcodes and text remain readable under typical lighting conditions and scanning workflows.
- Be strategic about label placement. Avoid positioning on high-friction zones or tight curves that can cause peeling or distortion.
Labeling With Purpose, Built for Performance
Your label ensures compliance, protects patients, and keeps your supply chain flowing. And whether your product is used once or a hundred times, its label should support that mission.
Electronic Imaging Materials offers labels that go the distance. From rugged single-use device labels to advanced systems for reusable instruments, we offer:
- Materials that resist sterilization, solvents, and abrasion
- Adhesives tailored for your substrate and lifecycle
- Barcode systems that support full traceability and compliance
Reach out today and let’s build a labeling solution that works as hard as your device does.