You run a busy production line for diagnostic devices, each step painstakingly monitored for quality and safety. Everything seems in place—until you discover that vital information on the product’s label has faded after sterilization. Or maybe the label’s adhesive won’t stick properly to a device’s curved surface, risking noncompliance with medical regulations. Medical device labeling is more than printing stickers; it’s a meticulous process that can directly affect patient safety, regulatory compliance, and brand credibility.
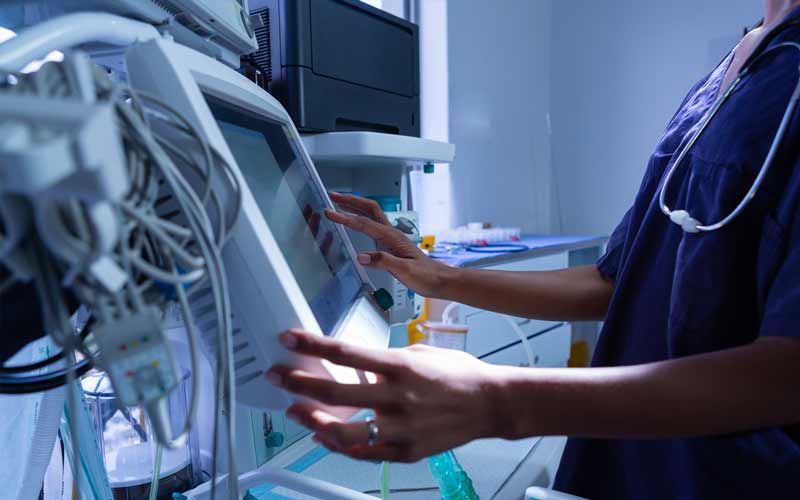
Challenge #1: Navigating Medical Device Regulation
Government bodies worldwide have stringent requirements for medical device regulation, focusing on traceability, safety, and quality control. Both the FDA (in the U.S.) and the European Medical Devices Regulation (EU MDR) specify what must appear on device labels—ranging from unique device identification (UDI) codes to hazard symbols.
How to Overcome It
- Stay Informed: Regulations evolve. Follow changes in labeling guidelines, especially if you distribute to multiple regions.
- Implement UDI or Equivalent Codes: Systems like UDI make it easier to trace devices throughout the supply chain. Invest in print and scanning technology that supports these codes reliably.
- Plan for Localization: If you market internationally, each region might have different language, symbol, or layout demands. Incorporate these requirements from the start.
Challenge #2: Durability Under Harsh Conditions
Many medical devices undergo sterilization processes—like autoclaving, ethylene oxide, or gamma irradiation—that subject labels to high temperatures, moisture, or chemicals. Even after packaging, devices may contact disinfectants, rubbing alcohol, or bodily fluids that can degrade standard label materials.
Ensuring Labels Survive
- Select Appropriate Facestock: Synthetic materials often outperform paper in high-temperature or chemical environments. Polyesters, polypropylenes, and specialized laminates are great choices.
- Use High-Quality Inks & Adhesives: Resin-based inks and adhesives rated for extreme conditions can keep labels readable after sterilization.
- Test Labels in Real-World Conditions: Don’t rely on generic specs. Simulate your device’s sterilization, shipping, and usage environments to confirm label performance.
Challenge #3: Maintaining Legibility Over Time
Labels might look great on the production floor, but frequent handling, incidental chemical exposure, or even prolonged storage can cause the text to blur. Over time, vital instructions or safety warnings can become unreadable, leading to misuse or confusion.
Legibility Best Practices
- Invest in Protective Coatings or Laminates: A clear laminate can shield printed text from scratches, moisture, and chemicals, especially if the label is color-printed or in constant contact with surfaces.
- Test Print & Ink Compatibility: Ensure your chosen facestock (label material) is compatible with your printing method, whether thermal transfer or digital printing.
- Prioritize Contrast: High-contrast design—like dark text on a light background—improves readability in low-light operating rooms or busy lab settings.
Adam C. | MediView
“Marissa Salisbury went above and beyond with our initial calls and then subsequent emails/calls. She has been a godsend and helped us make the best decision for our organization including pointing us in the right direction with UDI compliance.“
Challenge #4: Multilingual Requirements for a Global Market
Manufacturers distributing devices in multiple countries face complex language regulations. Labels must include instructions, warnings, and technical data in local languages, each with nuances of grammar and terminology. Incorporating all this data onto a small label without overwhelming the design can be a balancing act.
Streamlined Solutions
- Use Universal Symbols: Whenever possible, rely on ISO or globally recognized medical symbols to reduce text volume.
- Fold-Out Labels or Booklets: For devices needing extensive instructions, multi-page labels or extended content labels can fit multiple languages.
- Design With Space in Mind: Plan for text expansion in translations. Some languages require up to 30% more space than English for the same content.
6. Challenge #5: Space Limitations on Smaller Devices
Many medical devices, from catheters to hearing aids, offer limited labeling space. Despite the tight space, regulations demand specific details—UDI codes, usage information, and hazard symbols must all appear. Failing to include required data or making the label too small to read can quickly land you in noncompliance territory.
Overcoming Size Constraints
- Use 2D or QR Codes: These compact codes can store more data than standard barcodes, saving label space for text.
- Reduce Clutter With Smart Layouts: Distinguish essential data (like device identification) from supplemental info.
- Multi-Layered or Peel-Back Labels: Employ creative label formats that reveal additional information without crowding the surface.
If these common pitfalls sound familiar, now is the time to fortify your labeling approach. Whether you’re updating existing processes or launching a new product, having the right partner can make all the difference.
7. Additional Tips: Adhesives, Materials, and Testing
For medical device labeling, adhesive compatibility with the device’s surface is critical. Curved or irregularly shaped surfaces, like IV tubing or silicone implants, require specialized adhesives that remain firm yet flexible. Some adhesives are heat-activated, bonding more securely after a sterilization cycle, while others remain tacky in cold environments.
Vetting the Material and Print
- Coronation or Corona Treatment: For color printing, a corona-treated surface helps ink adhere better.
- Resin Ribbons: In thermal transfer printing, resin ribbons typically yield the most durable results for high-heat or chemical-prone environments.
Early Testing: A Must-Do
Before a full rollout, test labels under real or simulated conditions. Submerge labeled devices in disinfectant, expose them to repeated sterilization cycles, or store them in various temperature/humidity settings. This trial phase can reveal weaknesses in adhesive bonding or print clarity, enabling you to adjust before regulatory audits or large-scale distribution.
8. How Laboratory Barcodes and Labels Fit In
Laboratory barcode labels are essential beyond the lab. They provide a reliable method for tracking medical devices, managing inventory, and ensuring compliance in healthcare and manufacturing environments.
The Role of Laboratory Barcodes
Although barcodes are often tied to laboratory barcodes or laboratory labels, they also play a significant role in medical device management. When used on equipment or consumables, barcodes streamline supply chain tracking and inventory control, ensuring each item’s location, maintenance history, or usage rate is documented.
Labeling Beyond the Lab
Modern healthcare facilities often rely on digital scanning systems to avoid errors in device usage or stock replenishment. Whether you’re dealing with bandages, syringes, or implantable devices, a barcode-based approach can reduce confusion, expedite audits, and verify compliance more easily.
Keeping Medical Device Labeling Compliant and Clear
Medical device manufacturers have a lot on their plates: complying with strict medical device regulations, ensuring label durability in harsh sterilization processes, accommodating multilingual text, and fitting everything onto devices that may be smaller than a credit card. Underestimating medical device labeling can lead to recalls, damage to your reputation, or even patient safety risks.
Fortunately, these challenges are surmountable with thoughtful planning, the right materials, and thorough testing. Integrating best practices—like using robust adhesives, employing protective coatings, and verifying print durability in real conditions—helps you produce labels that remain legible and intact for the device’s entire lifespan.
Choose Electronic Imaging Materials as Your Partner in Reliable Labeling
Electronic Imaging Materials understands the complexities of medical device labeling better than most. Our team specializes in engineering labels designed to endure sterilization cycles, chemical exposure, and the tight spaces often found on modern devices.
- Tailored Materials: From specialized laminates to heat-resistant adhesives, we match each product’s demands with a suitable labeling solution.
- Proven Printing Technology: We help you choose or refine printing methods—like resin-based thermal transfer—that maintain crisp text and barcodes despite high-heat or high-moisture environments.
Don’t let labeling be the weak link in your product’s chain of care. Reach out and discover how our proven solutions can keep your medical devices compliant, legible, and safe—from production line to patient care, it is to maintain sample integrity and compliance, so we customize our labels and adhesives to suit your exact requirements. Ready to secure your lab’s future against mislabeled or unidentifiable samples? Get in touch with our team and discover how EIM can enhance your labeling process, saving you time, money, and unnecessary complications in the long run.