Have you ever printed out the perfect set of barcode labels only to find that they just won’t stay put? It’s frustrating when labels peel, slide, or completely fall off, leaving products, packages, or shelves unorganized and difficult to track.
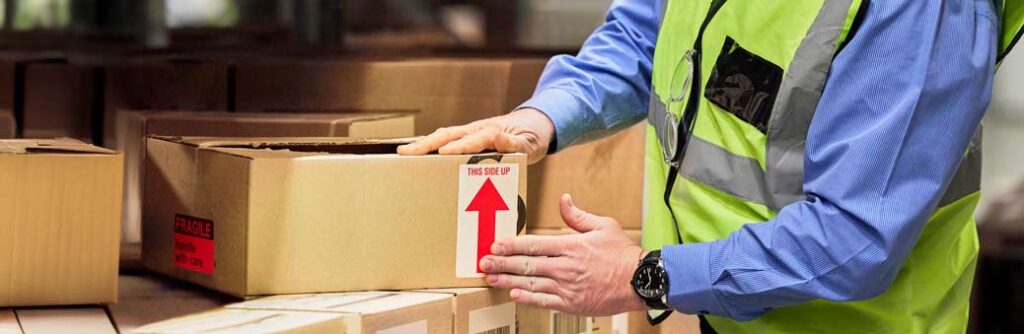
Whether you’re labeling inventory, assets, or shipments, having a label that sticks is crucial. So, what’s going wrong, and how can you fix it? Let’s walk through some common reasons why barcode labels don’t stick and what you can do to make sure your labels stay where they belong.
1. Surface Contamination
One of the most common reasons barcode labels fail to stick is surface contamination. When dirt, dust, oil, or moisture is present, even the strongest adhesive may struggle to create a bond. Surfaces that seem clean might still have invisible residues that make sticking tricky.
Make sure to thoroughly clean the surface before applying your label. Use a simple wipe with isopropyl alcohol or a clean cloth to remove any dust, oil, or moisture. Waiting for the area to dry fully is essential before sticking on the label. Barcode label examples like warehouse inventory adhesives may need extra cleaning if applied to equipment or storage shelves exposed to dirt or grease.
2. Improper Set Time
Some barcode labels require a specific set time to form a secure bond with the surface. This means you may need to wait at least 24 hours for the adhesive to fully cure and create a permanent hold.
Check your label supplier’s instructions to see if set time is a factor. If it is, give your labels the necessary time to bond completely before putting them to use. Rushing this process can result in labels peeling or shifting, especially if they’re subjected to movement or stress too soon.
3. Incorrect Adhesive Type
Not all adhesives are created equal. Labels can come with permanent, removable, or specialty adhesives that work best on specific surfaces and under different conditions. For example, a removable adhesive is great if you need to reposition labels, but it won’t hold up well on surfaces that require a permanent bond.
Evaluate your needs and pick the correct adhesive type (this is where having a Label Expert comes in handy). If you’re working in a warehouse, a strong permanent adhesive is often necessary for pallets or boxes. On the other hand, office settings might do fine with removable adhesives for temporary filing systems. If your barcode labels need to withstand extreme environments, consider specialty adhesives that are chemical or water-resistant.
4. Incorrect Material
Choosing the wrong label material is another common mistake. It’s important to know that adhesive and label material are different. The adhesive bonds the label to the surface, while the label material must be suitable for the environment where it’s applied. For instance, a paper label material won’t work well in a freezer, even if the adhesive is strong enough to stick in the cold.
Understand your environment and choose the appropriate label material. For outdoor applications, you may need a durable plastic or vinyl label. Barcode labels used in refrigerated warehouses should be made from freezer-grade materials to handle low temperatures. If your label will be exposed to sunlight, consider UV-resistant materials to avoid fading or peeling.
5. Temperature Issues
Temperature plays a significant role in label adhesion. If the surface or the environment is too hot or too cold, the adhesive may not work as intended. For example, applying a standard label in freezing conditions will often result in failure.
Check the temperature recommendations for your barcode labels before applying them. If you’re labeling in a cold environment, opt for labels specifically designed for low temperatures. In high-heat settings, like labeling machinery that heats up, choose heat-resistant labels to ensure they don’t lose their hold.
Get the breakdown on the science of adhesive labels, including the four layers of labels and how they work together to create a practical label for your specific needs.
6. Incidental Chemical Exposure
Sometimes, barcode labels are exposed to chemicals that weaken the adhesive. If labels are occasionally splashed with gasoline, cleaning solvents, or other harsh substances, they may degrade over time, causing them to peel or lose legibility.
If chemical exposure is unavoidable, choose labels designed to be chemical-resistant. For instance, barcode labels in laboratories or chemical plants need to be able to withstand splashes or spills. Look for materials and adhesives that are built for durability in these tough environments.
7. Surface Texture
The texture of the surface you’re labeling can also make a difference. Smooth surfaces generally allow for better adhesion, while rough or uneven textures create gaps between the adhesive and the surface, reducing the bond strength.
For rough or uneven surfaces, consider using a label with a more aggressive adhesive. These adhesives are designed to grip better, even when the surface isn’t perfectly smooth. Examples include industrial barcode labels for rough wooden pallets or textured plastic bins.
8. Application Pressure
When applying a barcode label, the amount of pressure you use matters. Insufficient pressure can prevent the adhesive from spreading evenly and bonding to the surface.
Press down firmly and evenly on each label after application. If you’re using a machine to apply labels, make sure it’s calibrated to apply the correct amount of pressure. Whether you’re using a sticker or label for a shipping box or a piece of equipment, a simple, firm press can make a big difference.
9. Moisture or Humidity
High moisture or humidity levels can interfere with a label’s adhesive properties. If the surface is damp or the environment is very humid, labels may not adhere properly or could start to peel over time.
Dry the surface thoroughly before applying a label, and consider using moisture-resistant materials for environments prone to humidity. In wet conditions, synthetic labels, like polyester or polypropylene, perform better than paper labels.
10. Environmental Exposure
Environmental factors like wind, rain, and sun can impact a label’s performance. Outdoor labels need to be able to withstand these elements for an extended period.
Use weather-resistant labels for outdoor applications. These labels are designed to handle UV exposure, rain, and temperature changes. For example, barcode labels used for outdoor equipment tracking need to be made from durable, weatherproof materials.
The Bottom Line
Barcode labels are vital for keeping businesses organized, but when they don’t stick, it can cause major headaches. The good news is that understanding common problems—like surface contamination, incorrect adhesive type, or temperature issues—can help you choose the right labels for your needs.
Take the time to assess your labeling environment and requirements. Whether you need freezer-grade labels, chemical-resistant adhesive, or outdoor-friendly options, selecting the right label and adhesive combination is key to long-lasting performance.
When in doubt, test your labels before making a bulk order. Understanding how labels behave in your specific setting can save you time, money, and frustration. After all, a barcode label that stays put is essential for smooth operations in any business.
Let EIM Create Your Next Label
Frustrated by labels that just won’t stay in place? At EIM, we offer high-quality, durable barcode labels and custom solutions built to withstand the toughest conditions. Connect with our team today for expert guidance and free label samples designed to meet your specific needs.