Have you ever wondered what gives labels their sticking power? How do bumper stickers manage through harsh winters, yet sticky notes permit a movable & reusable application? The answers lie within the type of adhesive. In its simplest definition, the adhesive is responsible for bonding two surfaces together. But given the number of options and types of adhesives available, discovering which to use for your own labeling application may prove to be a tricky process.
> Feeling educated? Speak to The Label Experts today!
> Check out this infographic on how to properly apply label samples!
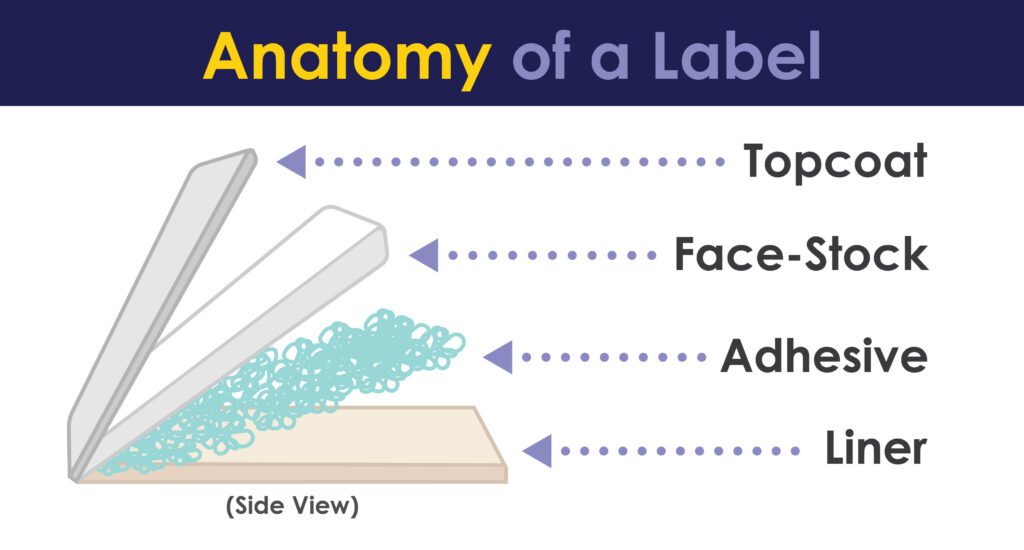
Ask Yourself the Right Questions
To help narrow your search for the proper adhesive, try answering these three basic questions first:
1. What type of surface do I want to bond to?
Will you be bonding to glass, polyester, steel, or wood? Perhaps even foam or rubber? The features of these surfaces will guide you to the appropriate adhesive. Smooth vs. rough, curved vs. flat, dry vs. moist. These are important properties to consider moving forward.
2. What material do I want to bond with?
The substrate, or material, is another important factor. The adhesive may need to be strong enough to hold a metal nameplate, or perhaps stick to a plastic that needs laminating. The function of your label plays a key role as well. Does the label need permanent positioning or will removability be required?
3. What are the conditions the bond must withstand?
Understanding the end-use of the label is critical to knowing how much specialty is needed. Typical indoor applications may be easily solved by most general adhesives, but what about exposure to outdoor conditions? A specialty adhesive may be more appropriate. Extreme temperatures, weather, sunlight, grime, chemicals, and water are all external conditions to consider when labeling your surfaces.
Meet the Adhesive Families
Pressure-sensitive adhesives are generally grouped into three families based on their chemical makeup. Acrylic, rubber, and silicone comprise the liquid glues that are used on all of our products. Knowing the benefits and trade-offs one type has over another can offer insight into your own labeling needs.
Rubber | Acrylic | Silicone | |
---|---|---|---|
Initial Bond Time | Fast | Moderate | Slow |
Variety of Surfaces | Most | Many | Specialized |
Common Application | Typical Indoor | Outdoor | Extreme Conditions |
UV Resistance | Fair | Good | Excellent |
Chemical Resistance | Fair | Good | Excellent |
Temperature Resistance | < 300°F | < 400°F | < 600°F |
Expense | Low | Moderate | High |
Know Your Properties
Now that we’ve learned about the types of adhesives available, there are a few other minor things to consider.
After receiving your free samples, you may be tempted to choose one adhesive over another because it feels “gooier” or stickier. This is a common mistake! The stickiness of the adhesive, or the tack, is just one measure of an adhesive’s performance. As the tack increases, other crucial dimensions of the adhesive will decrease. This includes the shear, the internal chemical strength, and the peel adhesion, the bond created after applied pressure. Adhesive’s overall performance is evaluated under these conditions, so it is important not to be tricked into falling for an unnecessary amount of goo for little use. After all, you may end up with the dreaded “adhesive ooze” after applying to a surface, leaving excess mess around your label.
While our guide may be useful, nothing can replace speaking 1-on-1 with one The Label Experts. We can offer assistance to answer your custom labeling needs. Before consulting with us, check out this page and our complementary Getting Started guide to help steer you in the right direction. The more info you know about your application, the quicker we can match you to the right product. We are excited to assist you and help come to a solution for your unique labeling needs.