Heavy Duty Labels for the Toughest Applications
EnduraLabels are permanent heavy duty labels for rugged manufacturing environments. These industrial strength labels are built with an ultra-aggressive adhesive for a secure bond to the dirtiest and grimiest surfaces. Oil resistant labels and weatherproof labels do exist!
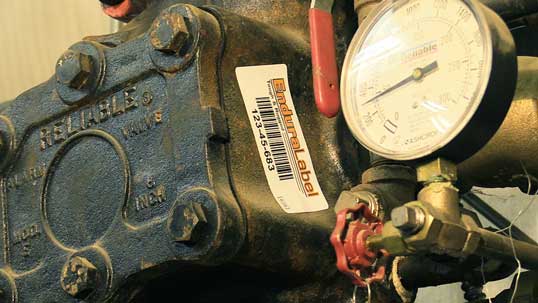
Product Highlights
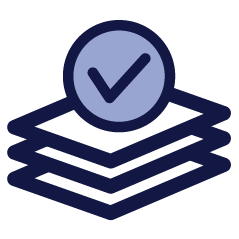
Tailored Designs
Specialty label adhesive perfect for dirty, greasy, or oily surfaces and equipment ID tags
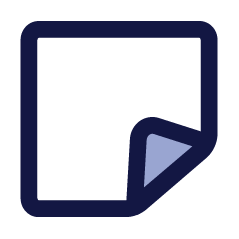
Durable Bonding
Permanent bond to low energy and highly textured surfaces, including TPO plastics
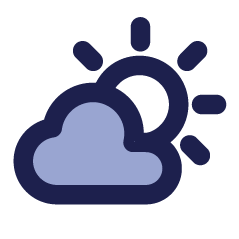
Weatherproof
Excellent weatherproof labels for all the elements
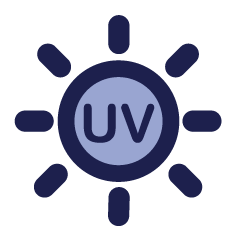
Outdoor Durability
Outdoor durable labels with a 2-year rating for UV and direct sunlight
Durable Material
Polyester material resistant to scratching, abrasion, and tears
Customization
Custom printed or blanks available
Full Color Printing
Full color, graphics, barcoding or simple text options
Flexibility and Control
Made-to-Order size and shape industrial labels
You can review product specifications below to determine which labels meet your requirements.
Still not sure which label is right for your application? We’ll send you free label samples to test >
Label Materials
-
628 White Polyester
Premium gloss white polyester with ultimate strength for long lasting bonds. -
629 Silver Polyester
Same great performance as 628, in semi gloss silver polyester. -
1778 Laminated White
Our 628 material gets pre-printed and laminated for outdoor usage and excellent resistance to chemicals. Thus creating one of our toughest materials. -
1777 Laminated Silver
Pre-printed and laminated 628 polyester in silver. Thus creating one of our toughest materials. Resistant to harsh chemicals commonly found in automotive and electronic industries.
What our customers are saying

Kristina M. | SafePath Products
“EIM has been outstanding from the very beginning. Joey, Noah and Erin have been fantastic to work with making our buying and set up experience almost effortless. I would highly recommend working with this team. They are very knowledgeable and highly professional. Thank you EIM team!“

Sonja T. | American Wick Drain Corporation
“I was looking for a label that would not detach from a “hard to label” material. The label is as durable as stated as well as meets our business needs.“

Jeswin R. | Roadside Systems
“Excellent customer service, easy to work with, high quality, and very communicative! We use barcode stickers on heavy-duty machinery. We’ve had no issues installing them and they stay stuck pretty well.“

Ted K. | Snow King Mountain Resort
“We’ve been using you guys for years and I am always very happy.“
We’re Ready To Help!
Talk With A Label Expert