Save Money with Visible Light
Now everyone wants to save money, right? Hope I’ve got your attention…
How long have you been using barcodes? More years than you can remember? If so, then you’ve definitely seen barcodes go from simple vertical bars to all sorts of shapes and sizes. Like barcodes, the label industry has seen a lot of changes (and improvements) in printing technologies, label materials and barcode scanning.
Back in the late 1970’s and early 1980’s, quiet, efficient thermal label printing equipment began to replace the noisy drum and hammer of old impact printers. At the same time, more and more barcode scanners were being developed, but back then, they often had very specific engineering that limited their scanning range and the types of barcodes they could read. Those were the days when we talked about “visible light” and “infrared” scanners rather than laser, CCD or image readers.
Those two types of scanners still exist today, defined by the wavelength of their light sources:
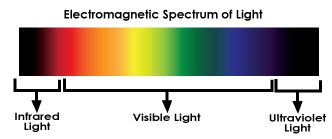
- Visible light scanners work up around 660 nanometers (nm). They are popular because you can actually see their red light and quickly align your scanner to a barcode. Another advantage of visible light scanners is that they can read barcodes printed in colors―not just black―particularly ones in the blue to green range that look black to the scanner. Lastly, barcodes can be printed with non-carbon based inks such as flexographic water-based formulas.
- Infrared scanners work anywhere in the infrared range of 1000 nm, beyond what the human eye can see. They are often used in more unique applications such as reading barcodes on photography negatives or for security labels with special red or black laminates used to prevent the photocopying of barcodes (like those found on ID cards). Carbon based inks are required, such as those found in thermal transfer ribbons.
To work in this new equipment, thermal imaging papers (aka direct thermal, or simply thermal papers) were developed as a cost effective way to print barcodes. These were especially appealing to the retail, shipping and healthcare markets. Thermal papers have a special chemical coating that turns black when heated, and other protective topcoats are added to shield against UV light, water, grease, and oil. Like the scanners, thermal papers are called either “IR” (short for infrared) or “direct thermal” which means they are only for visible light scanning. - Visible Light / Direct Thermal Papers are low cost and typically designed with medium to high sensitivity characteristics, which refers to the amount of heat needed to transfer an image. A good selection of materials and adhesive combinations has been created in response to the popularity of the visible light scanners.
- IR Papers are coated for high sensitivity printing and can be scanned in a broad range of wavelengths anywhere from 633 nm to 1000 nm. They are more expensive but the fact that they can be scanned with both visible light and IR scanners is a definite advantage. Unfortunately, only a limited variety of IR Papers have been developed.
Getting back to all those changes we mentioned… there have been constant improvements in barcode scanners so that they can now “auto-discriminate”―a fancy word for being able to read all types of barcodes. Not only can they handle lineal codes like Code 39 or Code 128, but also 2D (Two-Dimensional) codes like PDF417, Data Matrix and the “newest kid on the block,” the QR Code. Some scanners have also improved to be able to read barcodes at a distance of 50+ feet. These days, most infrared scanners have been replaced with visible light units.
Label manufacturers continue to seek better print quality and label durability. Electronic Imaging Materials, Inc. is right in there, working to make it faster and easier for our customers to get the labels they really need. We are constantly updating and adding to our arsenal of printing equipment, moving from simple black on white systems to high-speed, high-quality, full-color commercial units.
EIM also does ongoing research and development to provide the right materials for newer printing systems and special labeling applications. At the same time, we all want to control costs. Our selection of label materials is mind-boggling, so we do regular cost control assessments, not only in regards to labels, but in our manufacturing processes, too.
After doing direct thermal market and product analysis, we are going to suggest―to anyone still using IR Paper, and especially to those concerned about this tight economy―NOW is the time to make a change! Label Printers and Barcode Scanners have changed and so your label materials should change with them.
The cost of Visible Light (non-IR) Papers can be nearly 50% less than Infrared Papers, depending on your label application and the adhesive you need. They are also less susceptible to light degradation and can be used in any standard speed printer, whereas IR materials tend to require higher speed models. Print quality may be slightly different, so testing, perhaps with adjusted heat settings, is suggested.
If you have any questions about the differences between IR and Visible Light labels, or would like a quotation on your Direct Thermal Paper Label options, be sure to contact The Label Experts. They are ready to assist you and get you samples to test and compare.
Please Note: The differences we discussed in this article only pertain to direct thermal papers. Plastic labels used for direct thermal printing do not experience the same printing and barcode scanning issues.