Direct Thermal and Thermal Transfer Labels
Labels can be printed using several differing printing technologies. However, one of the most popular methods is called thermal transfer printing which uses roll-form labels and printing ribbons. This technology requires lower heat settings to transfer a printed image than some printing methods such as a laser toner process. For this reason, you have the widest variety of paper and film label materials at your disposal, including an extensive choice of label adhesives to fit special labeling applications.
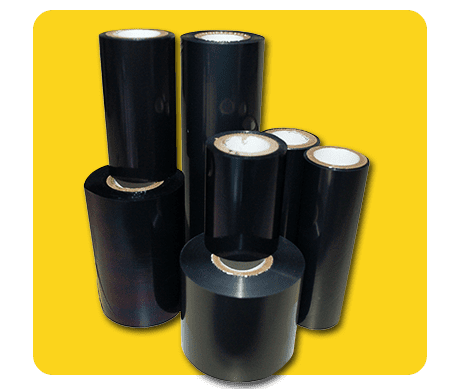
Finding the right printing ribbon
> Want a more condensed version? Check out this infographic!
We can’t stress enough how important it is to choose the right thermal transfer ribbon formula for your labels and the right format for your label printer. The bond achieved with a well-matched printing ribbon to a label substrate is critical. With the right ribbon and printer settings, you get the best print quality and durability, sometimes even avoiding the need for a protective film laminate.
Unlike many suppliers, Electronic Imaging Materials, Inc. doesn’t handle just one line of ribbons. Instead, we have a thorough cross-section of high quality ribbons made by some of the most trusted companies in the ribbon industry. We also thoroughly test every ribbon and label material we sell to assure the highest compatibility and durability.
While the ribbons that we offer on our Web Store are formatted to fit the Zebra and TSC printers we sell, we also have ribbons for other popular printer models including Datamax, Intermec, Monarch, Saito and many others.
The Right Formula
Thermal transfer ribbons are classified in three categories: Wax, Wax/Resin and Resin.
If you think of them in that order, they basically match the three general classifications for label materials: paper, mid-range, somewhat soft synthetics and glossy, hard films like polyester. Within the three ribbon categories, ribbon manufacturers offer an extensive choice of ribbon formulas to fine-tune print results on specific materials. Not only do they address smudge and scratch resistance, but many handle specific conditions involving chemicals, solvents, and temperature extremes. Initially designed for bar code printing, black thermal transfer ribbons predominate. For label impact, color coding and attractive graphics, some manufacturers have also developed a good selection of colored printing ribbons based on Process CMYK and spot colors.
> See our article with more Information About Ribbon Formulas
The Right Format
With the popularity of variable printing and the need for durable labels:
If you think of them in that order, they basically match the three general classifications for label materials: paper, mid-range, somewhat soft synthetics and glossy, hard films like polyester. Within the three ribbon categories, ribbon manufacturers offer an extensive choice of ribbon formulas to fine-tune print results on specific materials. Not only do they address smudge and scratch resistance, but many handle specific conditions involving chemicals, solvents, and temperature extremes. Initially designed for bar code printing, black thermal transfer ribbons predominate. For label impact, color coding and attractive graphics, some manufacturers have also developed a good selection of colored printing ribbons based on Process CMYK and spot colors.
> See our article with more Information About Ribbon Formulas
This is where EIM comes to your rescue
Once we have defined the best label material for your application, we can easily recommend the best printing ribbon. All we will need to know is the name of your printer and the model number. Contact The Label Experts for assistance with your ribbon selection.